Ingersoll-Rand Aktie
WKN DE: A0NEQZ / ISIN: IE00B6330302
17.04.2006 14:47:00
|
Bobcat Goes Lean With Menlo Worldwide
SAN MATEO, Calif. and WEST FARGO, N.D., April 17 /PRNewswire-FirstCall/ -- A major re-engineering project to improve warehousing operations and inventory accuracy, while streamlining material flow to assembly lines is already yielding benefits for the Bobcat Company, thanks to a new manufacturing support center established with Menlo Worldwide that has adopted "lean" warehousing concepts.
Like many major manufacturing concerns, Bobcat, a West Fargo, ND-based producer of small loaders, excavators and other compact construction equipment, is faced with an increasingly competitive global market where improving inventory accuracy and material flow management had become crucial to manufacturing efficiency - and customer satisfaction.
Six months ago, the company made a decision to outsource its warehousing and inventory support operations to Menlo Worldwide. "We wanted to focus on what Bobcat does best: designing and manufacturing the mini-excavators and other machines that our customers want, and growing the business," said John Mark Shaw, senior business unit manager, material support center and PPIC for Bobcat. The company had earlier started to use lean manufacturing techniques and wanted to install similar processes for its receiving, warehousing and material planning operations as well.
That's where Menlo came into the picture. Says Shaw: "We decided that an outsourcing approach was the best strategy for us. We looked for a partner whose core competency was lean warehousing and inventory reduction techniques as a core competency, and who could meet our three priorities: safety, timely receipt and delivery of parts, and quality."
It was the first time Bobcat had outsourced any of its logistics functions. "That was an innovation for us: we chose to draw on the expertise, resources and experience of Menlo to run this key operation instead of doing it ourselves," said Shaw. "One benefit was that we got a solution up and running quickly that began to deliver results almost immediately."
Redesigning the process
Previously, Bobcat was managing its receiving, inventory and material handling over a 10-acre outdoor area next to its plant -- which presented a number of challenges, not the least of which was weather. "Our business had outgrown the old methods for receiving parts and managing inventory," Shaw explained. Shaw and his management knew that the process could be improved -- and would have to be if the company were to meet its goals for growth and the surging customer demand for its products.
After evaluating a number of firms, Bobcat selected Menlo and awarded a contract in September 2005. A joint implementation team was formed, resources and facilities secured, and current inventory management functions and material flow practices mapped and analyzed. In November 2005 Menlo opened a new manufacturing support center for Bobcat in nearby Bismarck, ND and launched the initial redesign of material flow and inventory control processes.
The solution established a dedicated warehouse facility where Bobcat's receiving, inventory control, and material handling were centralized, reorganized, and adapted to lean warehousing methodologies. In the first five months of operations, overall inventory accuracy improved from 60 to 99 percent. The Dollar value of on-hand inventory was reduced by 26 percent. Parts shortages were reduced by 90 percent. And expedited freight costs declined by 95 percent. "Overall, we've made our supply chain more flexible and accurate, and in the process, wrung out a lot of waste and unnecessary costs," said Shaw.
Starting at the source
Menlo and Bobcat jointly designed the new solution using a principle called "line-side back." This approach, which ties in with lean philosophies of listening to the people who do the work, starts on the manufacturing floor, with the operators on the assembly line. It's intended to examine how the operators work, and using their knowledge and insight, create a plan for picking, staging, sequence and flow of goods to the operator that supports the most efficient methods of production.
The process drills down into specifics, such as how parts are packaged and presented to the operator, and even the types of racks used to convey the parts to the work "cell," and position them for ease and efficiency of access.
The plan is continuously reviewed and adjusted through "Kaizan" events -- essentially a formal, structured re-evaluation of a work activity. These events are conducted by teams of employees who do the actual work, facilitated by a manager. The teams review their original assessment, going back through the activity and how it is performed, looking for further opportunities to streamline and remove waste. "Kaizan" events are not one-time exercises, they are conducted on an ongoing basis with the client and are the methodology by which Menlo's and Bobcat's employees continually work together to save money and improve performance.
From line-side to warehouse
"Once we understand, with the operator's input, how best to set up the work cell on the assembly line, we work back to design the material flow between the warehouse and the plant to optimize that work cell and the operator's tasks," says Jeff Rivera, Menlo's director of automotive warehousing "We might design parts in kits, have them delivered in a particular frequency, set them in a specific sequence on racks, even help the operator redesign the workspace to be more efficient.
The goal is to have the right parts at the right place and right time available to the operator and then used in the assembly process to achieve the most efficient production possible. "A key point for the operator is to have the optimal 'ergonomic' presentation of parts," explained Rivera. This means designing material arrival, sequencing and presentation to minimize, for the operator, the amount of walking, bending or unnecessary movements required to take parts and then assemble them on the line.
Following the "line-side" assessment, Menlo then designs the ideal layout for parts in the warehouse, emphasizing safety and efficiency; establishes optimal material flow processes, and structures warehouse activities such as picking and kitting, staging of goods and how goods are actually packed, trucked and sequenced for delivery to the line. The goal: maximize inventory accuracy and efficiency of warehouse operations, and accurate, timely delivery of parts to the manufacturing floor.
The overall principle reflects one of Menlo's primary goals: to help Bobcat improve "first time through" quality, which is building machines that come off the assembly line the first time without defects. Noted Bobcat's Shaw: "This is crucial to improving our production processes. It cuts lead time to the customer, speeds output, and makes us more responsive and efficient."
In addition to supporting Bobcat's goals for "first time through" quality, Menlo also is examining other opportunities to apply lean principles, such as increasing throughput of the line using the same footprint. "What we do on the inventory control and lean warehousing side aligns perfectly with Bobcat's lean manufacturing practices. Both are focused on removing waste. And both are continuous. We've just scratched the surface," explained Rivera.
Problem-solving tools
Menlo and Bobcat are making extensive use of problem solving tools to identify and permanently remove waste. These techniques look at the root cause for an error, analyze the problem, then change specific, individual processes to correct an action and prevent the error from repeating. It's a closed-loop process that once a fix is initiated, it's tracked going forward to make sure the problem does not recur. Another tool is value stream mapping. The principle behind this is to "map" the flow of information and physical goods through a warehouse and into the plant, then take the process apart, and redesign it for improvement. It's not a one time exercise; such mapping is done again and again to drive continuous improvement and elimination of waste.
The Menlo operation supports four main Bobcat products. Today, orders are received at the Menlo facility, built into truckload shipments, and then delivered at regular intervals and precise times during the day to the plant. Parts are then "pre-staged" inside the plant for a short period before being delivered to a specific assembly point and operator on the production line.
Menlo and Bobcat already have identified one improvement opportunity. That's to eliminate the "pre-staging" of delivered orders in the plant. This will enable racks of parts, sequenced in a specific order, to move directly from the truck at the receiving dock to operator's cell on the plant floor without delay.
Shaw noted as well another area ripe for improvement: supplier conformance. "We're looking at how we can get our suppliers to adopt more standardized processes," he said. "This gets to how we receive parts, how they are packaged, how they invoice us, the types and amount of information we receive, the method of receipt, technologies used, etc. It's another big area where we can drive out waste."
Generating results
The outsourcing project has enabled Bobcat to gain benefits in the following areas:
-- Reduced costs for expedited transportation and lower, more predictable expense for regular freight service -- More consistent service from transportation providers -- Reduced production line shutdowns due to parts shortages -- Improved on-hand inventory accuracy and fulfillment, which reduces overall inventory costs and enables more precise production planning -- Reduced costs from inventory loss, damage and unusable parts which were scrapped due to improper storage or handling What you measure is what you get
As part of its solution for Bobcat, Menlo implemented inventory management and visibility systems that enable the manufacturer to have much more timely access and visibility to inventory and warehouse data, as well as performance metrics. The project is tracking against 26 different key performance indicators which monitor an equal number of Menlo and Bobcat work streams. The metrics are used to evaluate performance against goals, identify discrepancies, and generally give both production planning and inventory control the ability to understand performance in ways they were unable to before.
"What gets measured gets done," says Menlo's Rivera. "Lean methodologies center on two fundamentals: empowering employees to make change, and measuring what we do at multiple levels, continuously. Detailed performance metrics are the heart of the process. It's the magnifying glass that shows us where opportunities exist to further remove waste and find new areas where we can improve."
Extending the partnership
Menlo's responsibilities within the Manufacturing Support Center include: parts receiving and stocking, returnable container management, yard management, Kanban management, kitting and sequenced line-side delivery of parts and sub-assembled components to the manufacturing facility. This is the second Bobcat assignment for Menlo Worldwide. The company currently manages the supply chain serving Bobcat's manufacturing facility in Wuxi, China that receives parts from overseas suppliers.
Some of the biggest benefits the company is just beginning to see, says Shaw. "We now have a continuous improvement process that ties in our total supply chain, from supplier through receiving to the plant floor," he explained. "We are proactively creating an environment for improvement from the line side all the way out to the supplier." It's a coherent, proactive strategy that doesn't remove waste just one time, but finds opportunities over and over again. "That's powerful, and it demonstrates how a good partner with the right expertise and motivation can help guide you to improve in ways you never thought possible," concluded Shaw.
Menlo Worldwide, headquartered in San Mateo, California USA, is the US$1.4 billion supply chain services subsidiary of CNF Inc. The company manages a full range of logistics activities in North America, Europe and Asia for companies primarily in the automotive, technology, manufacturing, food and beverage, consumer product, chemical and retail industries. CNF is a $4.2 billion freight transportation, logistics, supply chain management and trailer manufacturing company. Further information about Menlo Worldwide and additional press releases are available via the Internet at http://www.menloworldwide.com/.
Bobcat's headquarters are in West Fargo, N.D. The company is a business of Ingersoll-Rand Company Limited , a diversified industrial firm. More information about Bobcat can be found at http://www.bobcat.com/ .
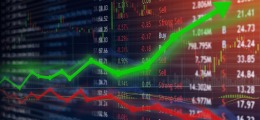
Wenn Sie mehr über das Thema Aktien erfahren wollen, finden Sie in unserem Ratgeber viele interessante Artikel dazu!
Jetzt informieren!
Nachrichten zu Ingersoll-Rand PLCmehr Nachrichten
Keine Nachrichten verfügbar. |
Analysen zu Ingersoll-Rand PLCmehr Analysen
Indizes in diesem Artikel
S&P 500 | 5 659,91 | -0,07% |